Fleet
Partner with the market leader in Service Bodies.
After pioneering the concept of service bodies in Australia in 1991, we have spent the next 30 years honing our craft. Using highly advanced sheet metal machinery, lean manufacturing and the latest technology, we produce high quality, reliable service bodies renowned for performance, even in the harshest conditions.
XL today is trusted by leading private and government corporations including Energex, Qantas, Rio Tinto, BHP Billiton, Origin Energy, Sandvik, Hastings Deering and Coca-Cola Amatil. XL has partnered with Telstra for almost 3 decades.
Add the following copy: For over 25 years, we have provided Telstra with Fleet bodies on Ford Rangers. We were one of the first companies to attain Ford Qualified Vehicle Modifier (QVM) status in Australia.
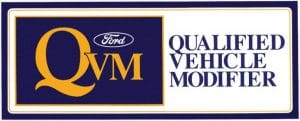
“In terms of quality, reliability, value and options – the whole package, no-one in Australia comes close.”
Andrew Harbison, COO of Isuzu Trucks Australia
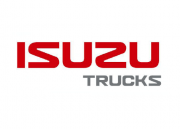
Peace of mind, Performance,
Reliability, Longevity
The XL Group provides logical, ergonomic service vehicle solutions that are fit for purpose and cost-effective and that offer excellent ROI. Our expertise in regulatory compliance provides customers with exceptional peace of mind that they can trust our team to deliver on both compliance and safety.
As Australia’s market leader in light vehicle service bodies, we consider it our duty to continually innovate and to set quality, safety and utility benchmarks at every turn.
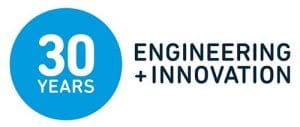
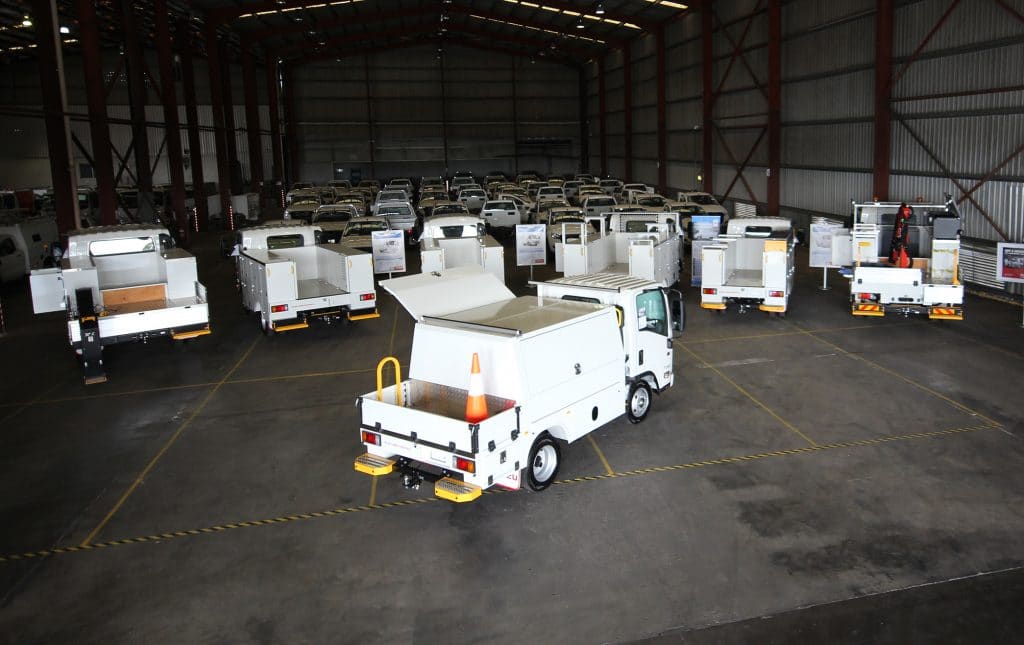
Why our Fleet clients have an advantage
State of the art production facilities and manufacturing processes.
The continual investment into cutting edge machinery, 3D modelling software and training staff in lean manufacturing allows XL to pass on savings to clients without compromising on quality.
The result is better quality, faster turnarounds, increased efficiencies.
Fully secured facility - the XL Mothershed
At 4000m2 the XL ‘Mothershed’ is large enough to store up to 150 vehicles undercover in a fully secured facility.
One of the fastest turnarounds on the market.
We’ve significantly improved our DIFOT.
It’s an area of critical importance to our Fleet Clients, as having increased certainty around DIFOT enables better planning, forecasting and improves operational efficiencies. We set ourselves a target of 85% DIFOT for June 2021, we reached 90% DIFOT in November 2020.
Repeatability – ease of parts replacement
Our automation technology enables precise replication, ensuring no fuss parts replacement.
XL bodies are tested beyond industry standards
We put our bodies through some of the toughest testing in the market.
The industry standard is 2 million vibrations, our Service Bodies are put through 3 million vibrations accelerated testing. Through Monash University, our bodies also undergo wind tunnel testing to evaluate and improve on wind drag coefficient.
The result is better quality, faster turnarounds, increased efficiencies.
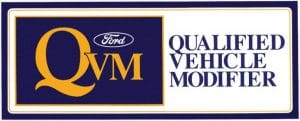
XL Service Bodies was one of the first companies to attain Qualified Vehicle Modifier status in Australia. As part of the process to attain QVM, Ford evaluated our procedures and build controls, along with quality control, vehicle safety standards, manufacturing process and controls, commitment to quality and continuous improvement, customer support systems and adherence to Ford guidelines.
This means our customers can be assured their XL Service Body is designed and manufactured to the highest standards.
“At Ford, we design and engineer a vehicle and then try to break it. We simulate 10 years of typical customer use in 6 weeks. We need to know it’s going to last.
We took a car to XL Service Bodies and put the service body on it…it was then put through a gruelling process of shaking. The car and the body held – it was quite impressive. This kind of thing instils confidence…we regard this commitment to safety and quality as essential, but it doesn’t always happen out there.”
Jeremy Welch, Strategic Projects, Ford Australia
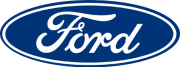
Our continual and significant investment in advanced manufacturing and the latest in automated machinery allows us to deliver a product of very high quality, consistency and reliability.
One of the fastest turnarounds on the market
We’ve significantly improved our DIFOT.
A key focus at XL over the last year has been the continual refinement of our systems and processes to greatly improve our DIFOT (delivery in full, on time). It’s an area of critical importance to our Fleet Clients, as having increased certainty around DIFOT enables better planning, forecasting and improves operational efficiencies. We set ourselves a target of 85% DIFOT for June 2021, we reached 90% DIFOT in November 2020. In such an unstable market, that level of certainty is a game changer for our clients.
Value for money – XL Service Bodies are renowned for their longevity.
Huge choice of 250+ Service Body Configurations
XL offers an unrivalled 250 different configurations of service bodies, more than any other provider nationwide.
For decades, we have successfully designed configurations to satisfy client demand across general, specific and even niche applications and distilled our learnings over an increasing array of industries and purposes.
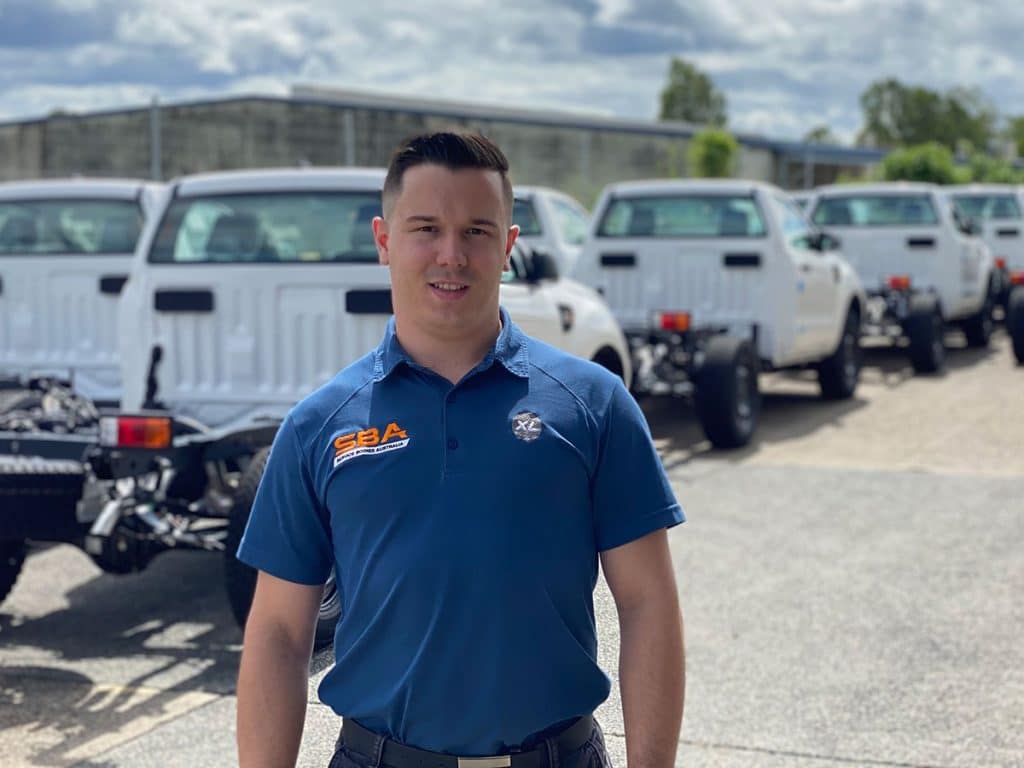
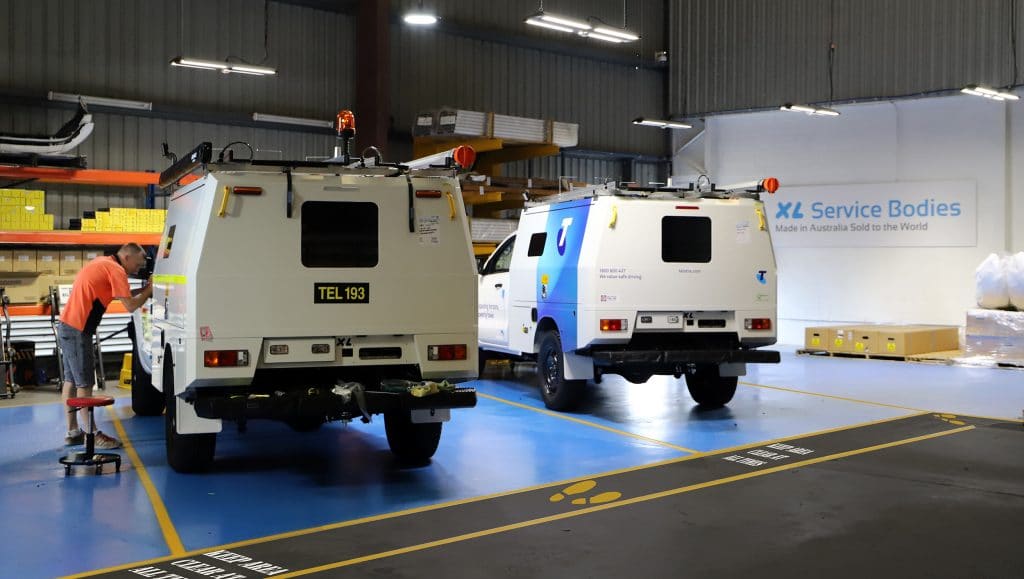
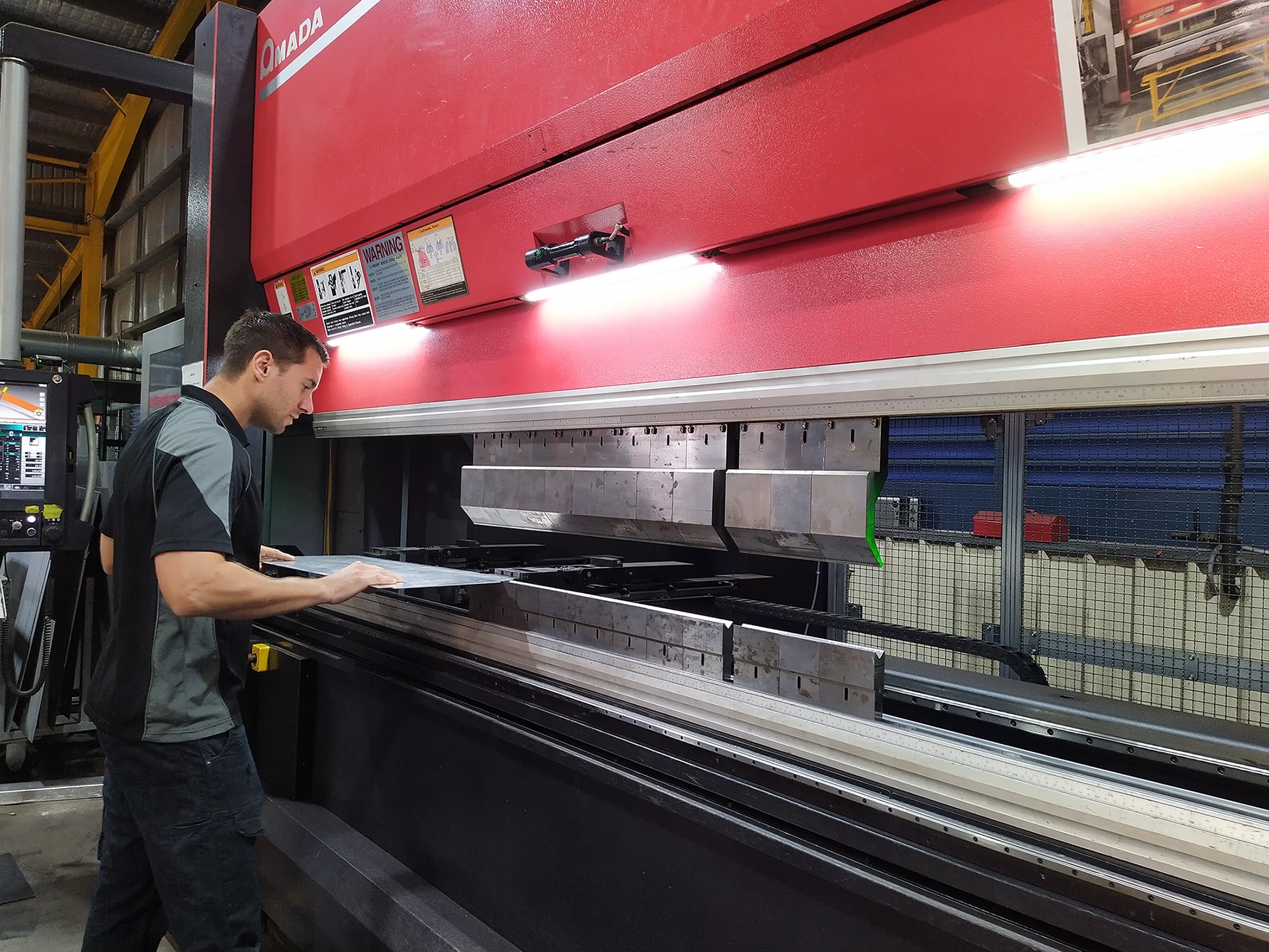
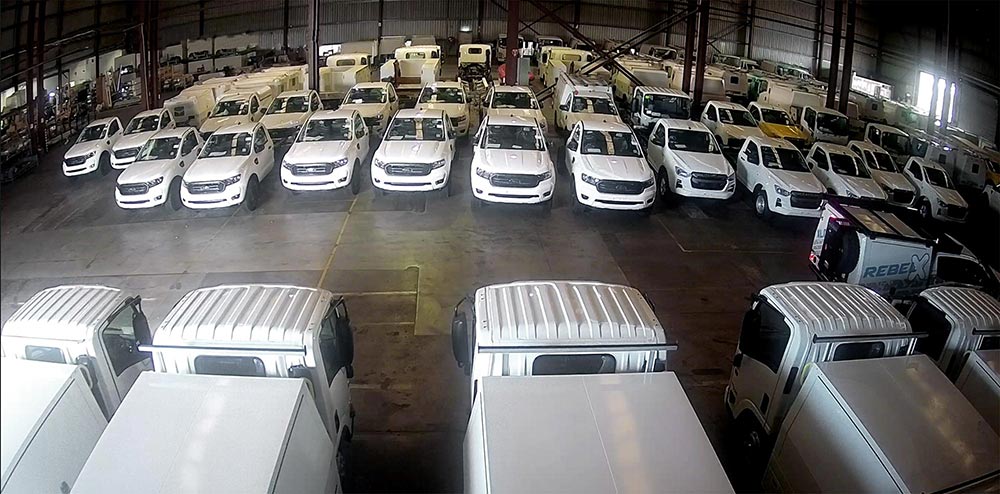
Advanced manufacturing, the latest in automated machinery
We are committed to continual innovation through investment in Advanced Manufacturing.
The machinery we use is best in the business and includes:
- Salvagnini L3 with 10 tower storage and Cartesian part takeout
- Amada Laser Cutting with Automation
- Amada Turret Punching with Automation
- Salvagnini P2lean panel folder
- Amada HG 10/3 Brake Press with Automatic Tool Change
- Amada HG 220/4 Brake Press with Automatic Tool Change
- In-house powder coating line.
Commitment to Australian components
Virtually all components are manufactured on site – a clear differentiator to many competitors who use imported components from China.
Large, diverse long-term staff
XL/SBA have a large, diverse staff and a workplace culture that values and rewards hard work, entrepreneurship, and innovation. The company’s commitment to delivering quality, continuous improvement and meeting the needs of staff and customers alike has ensured it remains the leading Service Body manufacturer in Australia.
Our Partners
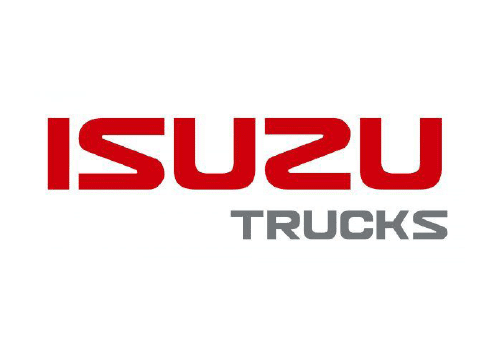
Isuzu Trucks
Since 2016, we’ve partnered with Isuzu Australia to provide them with the “Servicepack” range as the new addition to their Ready to Work line.
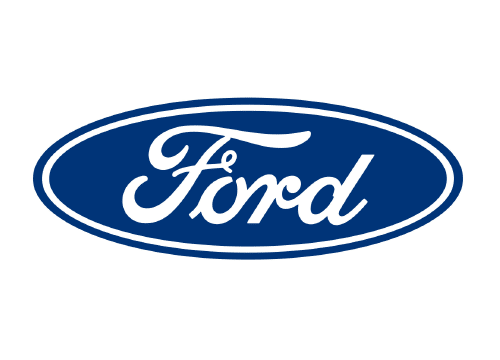
Ford Australia
We have carried out endurance testing of our products on Ford’s proving ground. We are also a Ford Qualified Vehicle Modifier (TBC)
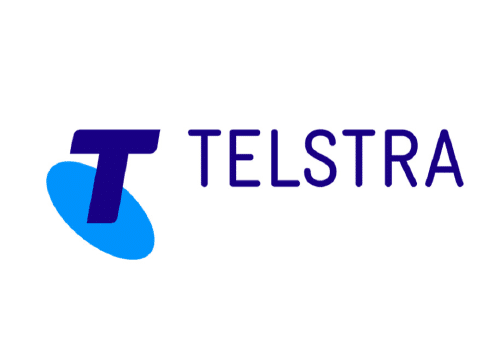
Telstra Fleet
Nearly three decades of continuous evolution in their fleet program.
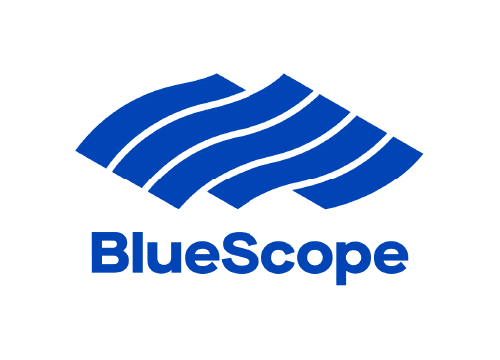
BlueScope Steel
XL has always insisted on locally manufactured BlueScope Steel as our first option in available raw materials.
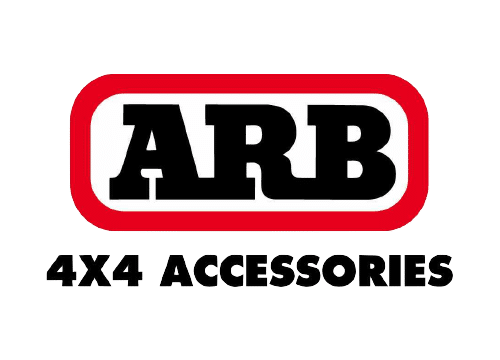
ARB Australia
Over twenty years of supplying and fitting aftermarket components.
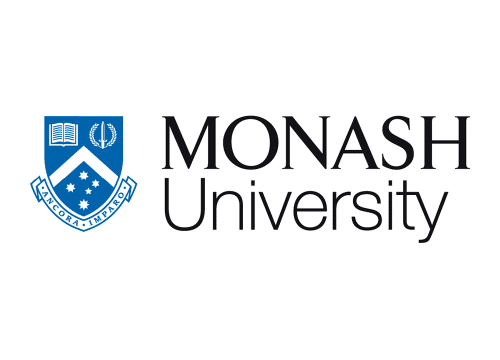
Monash University
Wind tunnel testing to evaluate and improve on wind drag coefficient.
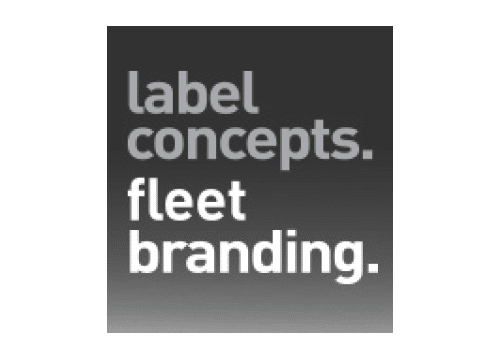
Label Concepts
Working with Label Concepts enables XL to offer a turnkey service including full vehicle/fleet livery.
Environmental/OHS
XL is committed to minimising our potential impact on the environment and providing and sustaining a safe and healthy workplace for our employees.
We reduce our environmental footprint through:
- Bulk recycling of material
- Reducing energy consumption (including installing 30kw solar panels)
- Minimising paper wastage
- Considering the environmental impact of any news tools and machinery
Additionally, over 95% of our manufactured products are recyclable.
OH&S
The XL Group complies with Work Health & Safety legislation at all times.
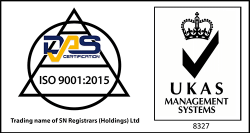
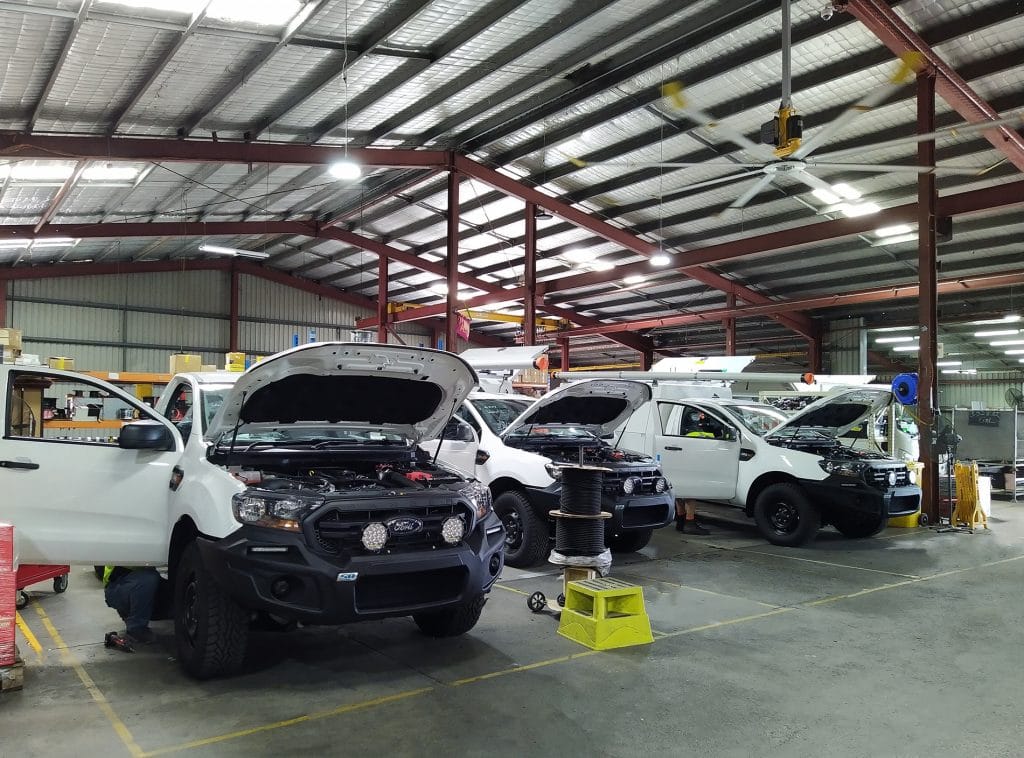
Interested in knowing more?
Call our Fleet Sales contact, Nathan Panitz on 07 3271 9911.